An economic tenet of Industrial Engineering is: When justifying a process change you first economically optimize the existing process, then economically define the proposed process and make your CBA’s (Cost-Benefit-Analyses) for both. Weighing each you will then derive your best course of action. Speaking from painful experience as a Manufacturing Process Engineer, you will make this mistake only once. Somewhere in a dark corner of a semiconductor facility (or hopefully a scrap pile) lies my personal ill-advised, sophisticated process equipment humiliation!
The makings of similar embarrassments are continually appearing within the component-driven hydronics heating industry. Hydronic component suppliers can be placed into three primary groups: boiler, distribution and radiation providers, corresponding to the three basic elements of the hydronic heating process. Component suppliers define the scope and applications of their products within a heating “system”, but that’s all. History and physics now can become excellent teachers.
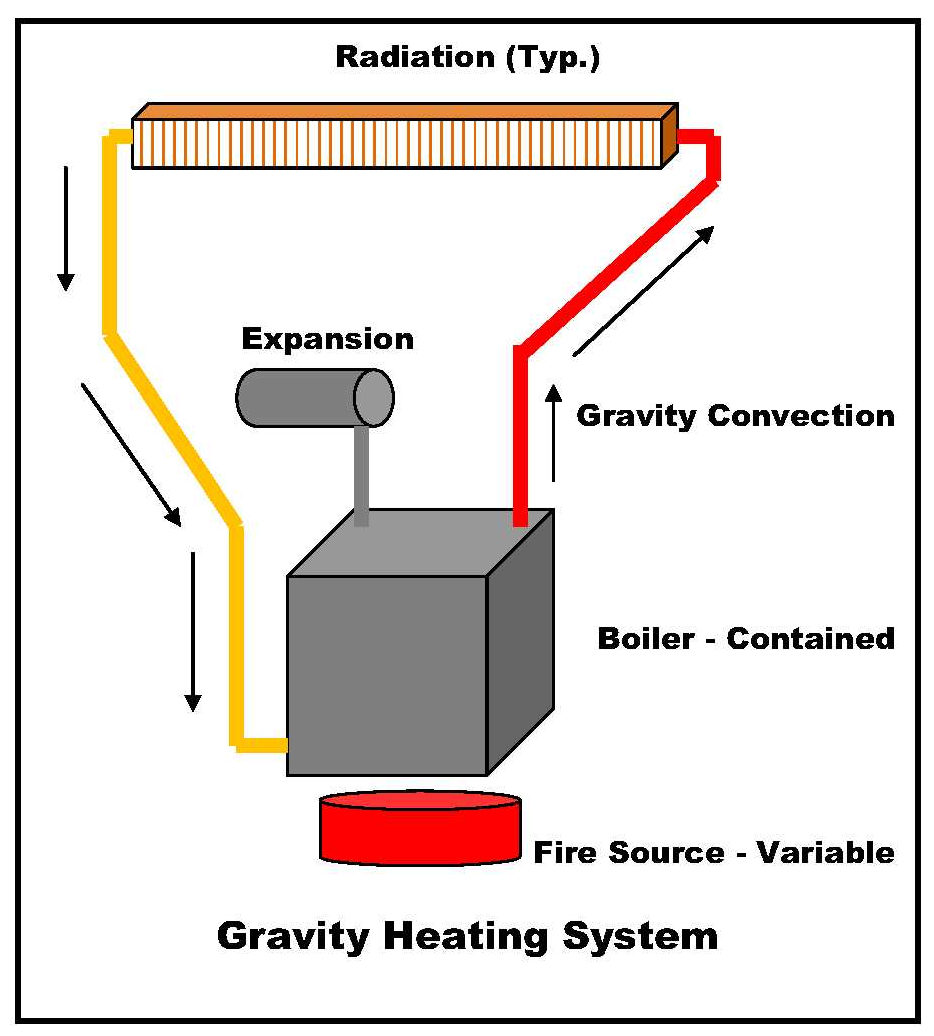
A century ago there were two competing water-based energy heating methods, Gravity Hot Water and Steam. Both were based upon the natural (gravitational) convection attribute of water in the liquid or the vapor state, respectively. Energy distribution from a boiler to radiation required no external energy, only variation of the fuel supply ….. more heat, more fuel. Powered burners and thermostats were added for control. Pumps (circulators) doomed gravity water by adding zone management while reducing costs. Thus the modern hydronic heating system evolved.
I’ve had the benefit of “playing with the pipes”, beginning as a teenager within our family heating business for over 70 years while pursuing a paralleled hi-tech engineering career. (You can’t raise ten kids even on an engineering day job.) So while doing hydronic work “on the side”, so to speak, hydronic evolution followed me. My “engineering hat” always questioned why natural convection shouldn’t be an asset rather than a flow-checked nuisance. The old “gravities” were so simple!
Post-engineering “non-retirement” provided time to aggressively play with hydronics. My “motor head” also makes me analogize heating systems with automobiles, i.e. the boiler being a pure “heat engine” with air, fuel and ignition for example. So when the delta-t circulator came along, there’s the “automatic transmission”. Now what can we do with the drive-line (distribution)? Can we re-evolve the Model T Ford car as a hydronic “Model Delta-T Appliance” by incorporating natural gravity convection into delta-t distribution? Well, we surely can and we have ….. !
The old Gravity Heating System featured a large boiler, proportioned larger piping and radiation, typically all cast iron and pipe. They were skillfully defined and installed, needed no distribution energy and lasted almost indefinitely, a tough act to follow. Its modern contemporary uses a much smaller (albeit more efficient) boiler, features multiple, circulated zones with smaller piping and radiation. Arguably it trades off fuel efficiency and convenience with increased distribution energy and “sophistication”.
The sophistication referred is almost entirely within the distribution element of hydronic heating systematization. This is the consequence of a component-driven marketplace, as prior mentioned. The contemporary build-in-place method of system installations relegates hydronic interconnection of boiler to radiation in particular as “The Plumber’s Playground” wherein there are few rules and little consequence. Every system differs in a similar application, and therefore all perform differently in practice.
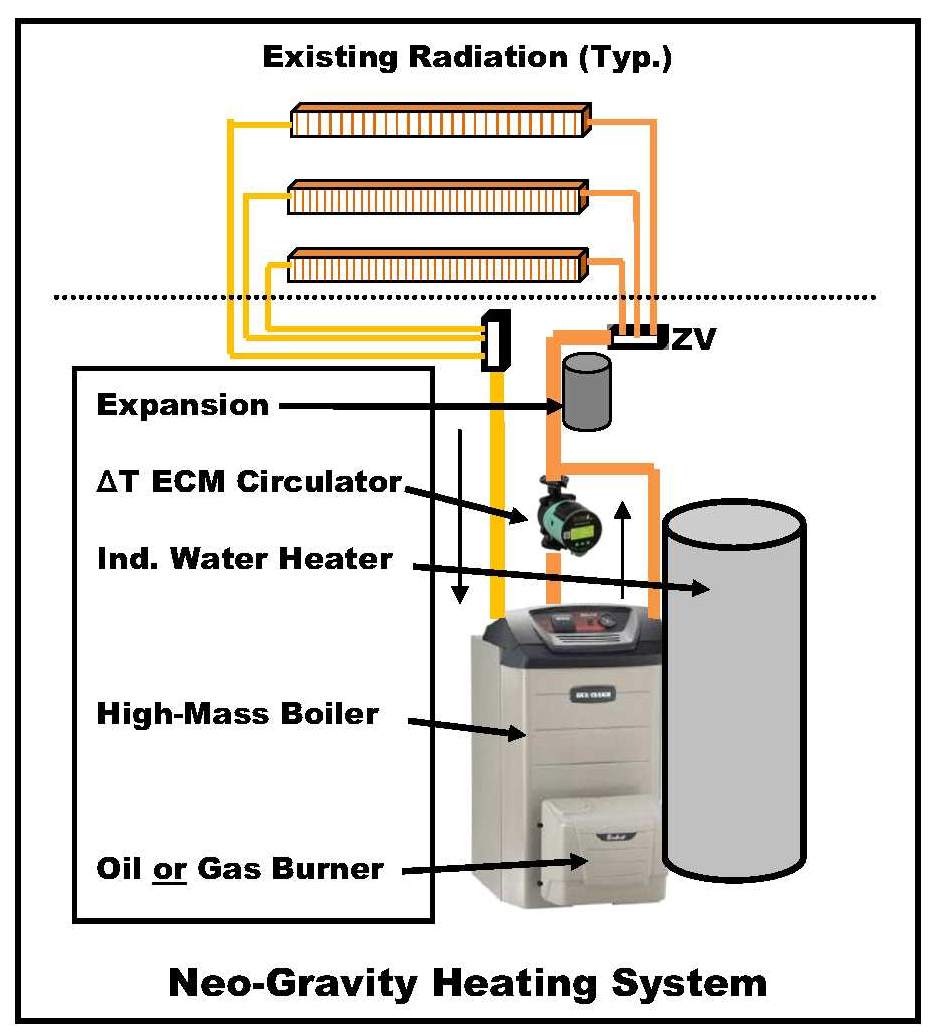
If the objective is to provide overall hydronic system energy efficiency including electrical power consumption, freelancing must be both qualified and quantified in practice. Redefining near-boiler piping to optimize natural (gravity) convection with the boiler and integrating a delta-t circulator to refine hydronic delivery dramatically reduces distribution material and energy usage. Our now-patented “appliance” exhibits a typical 8 to 13 Watts total distribution energy usage while heating, well over 90% reduction depending upon the contemporary configuration. Coupled with a high-mass, cast-iron boiler to enhance gravity operation, it also exhibits a thirty-plus year economic and operating life, twice or more that of low-mass, condensing units.
Further gravity convection enhancement is available within the appliance-to-zone interconnects. The “level & square, pipes everywhere” approach does not fly in the gravity world. Minimized, pitched piping to simple series and split perimeter radiation loops are ideal. Full port valving where necessary and fewest 90° fittings further contribute to minimizing head pressures and thus distribution energy consumption. It won’t win a beauty contest, but it will win the race.
Our 2,700 sq. ft. personally built (1970) raised ranch home has been our gravity test stand. An indoor wood boiler was convection-coupled to the cast-iron, flow-checked supply and circulator returned 3-zone “oiler” back in 1975. Multi-mode, multi-fuel operation has permitted completely unpowered, manually adjusted flow check wood gravity convection heating. As an example some years ago up here in “Frostbite Falls, NH” we were powerless from a severe ice storm for 10 days. A mere inconvenience for us ….. just feed it wood and adjust the valves.
We currently have a series of up to ten-year installed appliance “Beta Sites” that have now aggregated over 80 years service and 750,000 hours operation with no system-related calls! Two oil-contamination incidents did occur and last year a power line short-circuit blew out every control on a system. Our appliance is comprised of all standard, domestic trade components, so heat was restored within the day.
Our “appliance economics” haven’t been mentioned but are profound. Very significant complexity, material/labor content reduction and extended operating life vs. traditional architecture eclipse contemporary materials and methods. This observation was similarly but subtly affirmed in the 2019 Annual Boiler Report by several contributors opining that in effect it’s still hard to beat the economics of a well designed and installed cast iron boiler system. Their commentary and our natural (gravity) convection appliance development experience confirm that the prior cast-iron, i.e. the “pre-condensing boiler” process had yet to be optimized, to our peril. But try to find trade journalism and process development efforts to the contrary!
So, is history due to repeat? That is, will a hydronic “Model Delta-T” displace the heating industry’s “Carriage Makers”, or will there be yet another technical “skeleton” in my closet?
Updated 04/04/2025 P.D.M., Sr.